Good Manufacturing Practice, commonly referred to as GMP, is a set of guidelines and principles that ensure the consistent production and distribution of safe, high-quality products. These guidelines are applied across various industries, including pharmaceuticals, biotechnology, food and beverages, medical devices, cosmetics, and more.
Introduction
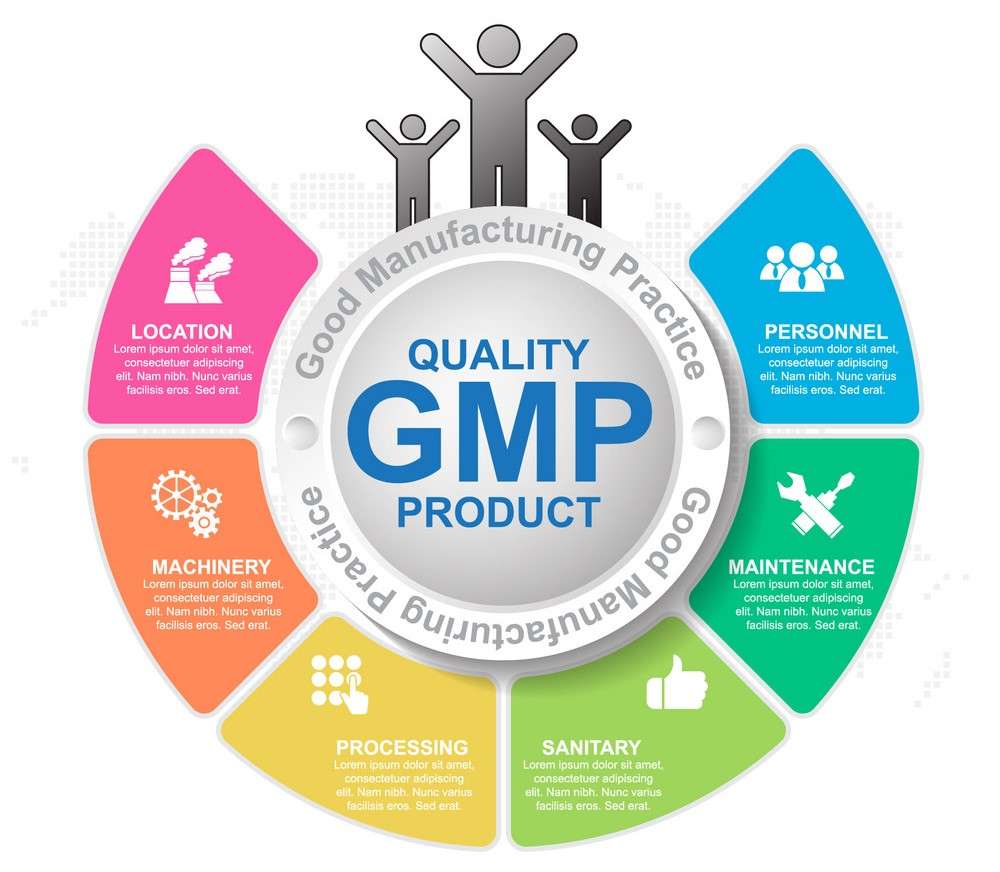
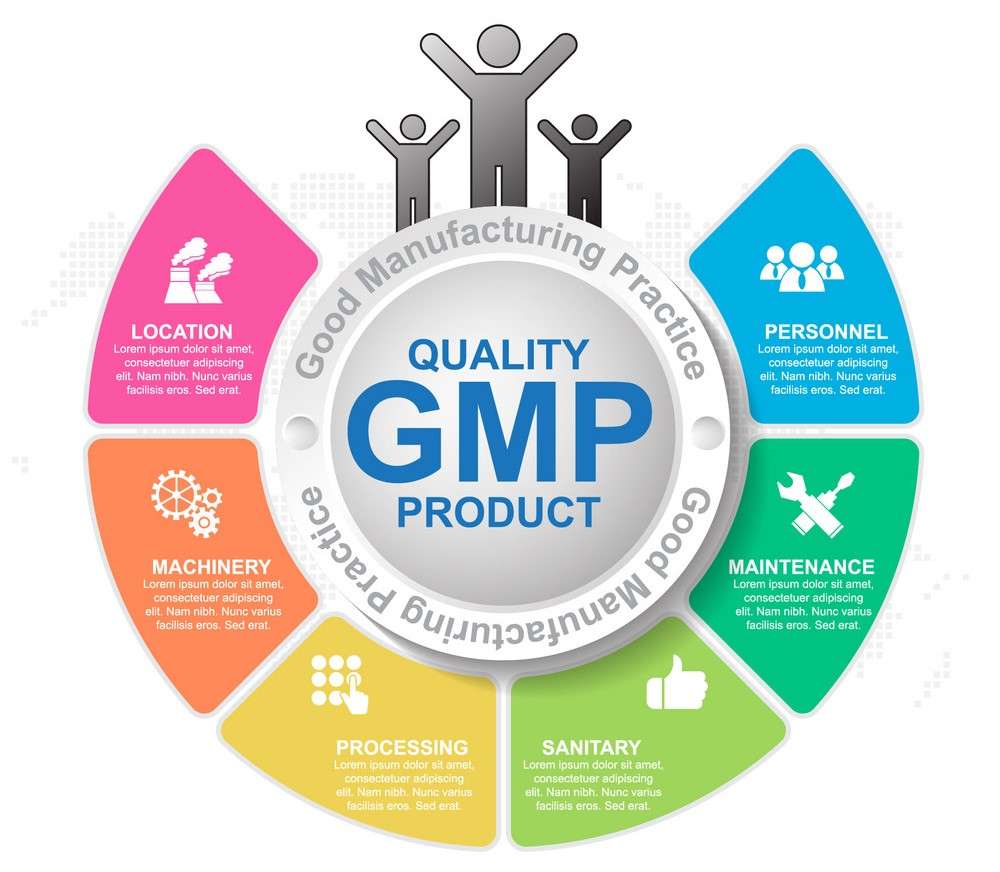
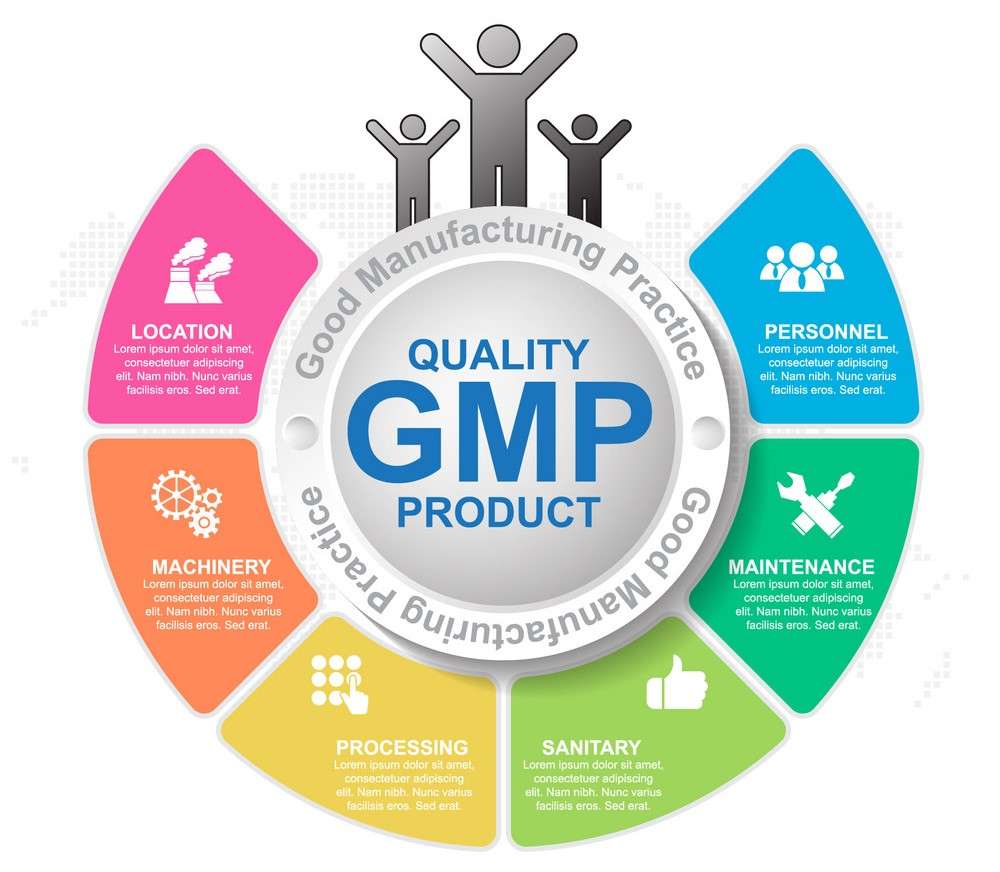
Historical Background
The origins of GMP can be traced back to the early 20th century, primarily in response to concerns about the safety and quality of pharmaceutical products. Over time, various countries developed their own sets of manufacturing standards. However, the need for a harmonized approach led to the development of international standards, notably the Current Good Manufacturing Practice (cGMP), ensuring a consistent and globally accepted framework for quality manufacturing.
Purpose of GMP
The purpose of implementing GMP is multifold:
- Consumer Safety: GMP ensures that products are safe for consumption or use by consumers. It mitigates risks related to contamination, mislabeling, and other potential hazards.
- Quality Assurance: GMP sets forth standards to maintain product quality and efficacy throughout the manufacturing process, guaranteeing a reliable and consistent end product.
- Compliance with Regulations: Adhering to GMP guidelines ensures compliance with local and international regulatory requirements, demonstrating a commitment to quality and safety.
Regulatory Framework and GMP Standards
Regulatory Agencies and Guidelines
1. International Council for Harmonisation (ICH)
The ICH is a global organization that brings together regulatory authorities and the pharmaceutical industry to develop harmonized guidelines for the pharmaceutical sector. ICH guidelines aim to standardize regulatory requirements, processes, and procedures, promoting international consistency in the quality, safety, efficacy, and use of pharmaceutical products.
2. Food and Drug Administration (FDA)
The FDA is a prominent regulatory agency in the United States responsible for protecting public health by regulating various products, including drugs, biologics, medical devices, food, and cosmetics. The FDA enforces GMP regulations to ensure the quality and safety of pharmaceuticals and related products.
3. European Medicines Agency (EMA)
EMA is the regulatory agency for the European Union, responsible for evaluating and supervising medicinal products. EMA’s GMP guidelines provide standards and requirements for pharmaceutical manufacturing, ensuring products meet specified quality and safety standards.
4. World Health Organization (WHO)
The WHO establishes guidelines on GMP to ensure the quality and safety of pharmaceutical products globally. These guidelines are crucial for improving the quality of medicines, especially in low- and middle-income countries, and promoting access to safe and effective treatments.
Key Principles of GMP
Good Manufacturing Practice (GMP) comprises a set of essential principles and guidelines that ensure the consistent production, control, and distribution of safe and high-quality products. Adherence to these principles is critical for maintaining product quality and safety throughout the manufacturing process. Below are the key principles that form the foundation of GMP:
1. Quality Management System (QMS)
Establishing a robust Quality Management System is fundamental to GMP. This involves defining and documenting quality policies, objectives, and responsibilities, as well as implementing procedures to achieve these objectives. An effective QMS emphasizes a process-oriented approach, risk management, and continuous improvement.
2. Personnel and Training
Ensuring that personnel are adequately trained, qualified, and possess the necessary skills and knowledge for their respective roles is a crucial principle. Training programs should cover GMP requirements, procedures, safety protocols, and the importance of quality in manufacturing.
3. Facilities and Equipment
Designing, constructing, and maintaining facilities that are suitable for the intended manufacturing processes and ensuring that equipment is qualified, validated, and maintained appropriately are vital aspects of GMP. Properly maintained facilities and equipment contribute to the production of safe and effective products.
4. Documentation and Recordkeeping
Comprehensive and accurate documentation of all aspects of the manufacturing process, including procedures, specifications, protocols, and records, is a key GMP principle. Effective documentation and recordkeeping enable traceability, consistency, and the ability to demonstrate compliance with GMP requirements.
5. Production and Process Controls
Implementing controls during production to ensure that processes are controlled, validated, and reproducible is critical. This principle involves monitoring and controlling all stages of production to achieve the desired product quality and consistency.
GMP Compliance and Audits
Principle | Description |
---|---|
Compliance Framework | Establish a comprehensive compliance framework encompassing all GMP principles. |
Regulatory Guidelines | Adhere to relevant national and international GMP regulatory guidelines and standards. |
Standard Operating Procedures (SOPs) | Develop and implement SOPs for every critical operation and process in line with GMP requirements. |
Training and Education | Conduct regular training programs to educate personnel about GMP principles and compliance requirements. |
Documentation Compliance | Ensure that all documentation is complete, accurate, and maintained in compliance with GMP guidelines. |
Recordkeeping | Maintain detailed records of all activities, processes, and quality control measures for traceability and compliance verification. |
Adherence to Specifications | Meet predefined specifications for raw materials, intermediates, and finished products, ensuring compliance with quality standards. |
Change Control Procedures | Implement robust change control procedures to evaluate and manage changes that could impact GMP compliance. |
Corrective and Preventive Actions (CAPA) | Promptly address and rectify any deviations or non-compliance through a systematic CAPA system. |
GMP in Pharmaceutical Manufacturing
Good Manufacturing Practice (GMP) is of paramount importance in the pharmaceutical industry, ensuring that drugs are consistently produced, controlled, and distributed to meet the quality standards appropriate for their intended use. Adhering to GMP guidelines is essential in pharmaceutical manufacturing to guarantee the safety, efficacy, and quality of pharmaceutical products. Below, we delve into how GMP is applied in pharmaceutical manufacturing:
1. Quality Management System (QMS)
A robust QMS is fundamental in pharmaceutical manufacturing. It involves establishing and maintaining a structured approach to quality, encompassing organizational structure, responsibilities, processes, and documented procedures that collectively ensure product quality throughout the manufacturing lifecycle.
2. Personnel and Training
Pharmaceutical companies must ensure that all employees involved in manufacturing activities are well-trained and competent. Training programs cover GMP requirements, specific job responsibilities, hygiene, safety measures, and quality awareness, empowering personnel to contribute effectively to maintaining product quality.
3. Facilities and Equipment
Pharmaceutical manufacturing facilities must be designed, constructed, and maintained to provide a suitable environment for the production of pharmaceutical products. Equipment used in the manufacturing process should be appropriately selected, validated, and maintained to ensure accuracy, consistency, and compliance with GMP standards.
4. Documentation and Recordkeeping
Accurate and comprehensive documentation is critical in pharmaceutical manufacturing. This includes recording and maintaining data related to production processes, testing, packaging, labeling, and distribution. Proper recordkeeping allows for traceability, accountability, and compliance verification.
GMP in Food and Beverage Industry
Principle | Description |
---|---|
Quality Management System (QMS) | Establish a QMS to ensure consistent production, control, and distribution of safe and high-quality food and beverage products. |
Personnel Hygiene and Training | Enforce strict hygiene practices and provide comprehensive training to employees to maintain cleanliness and prevent contamination. |
Facilities and Equipment | Design, construct, and maintain facilities and equipment to meet GMP standards, ensuring a safe and suitable environment for production. |
Sanitation and Cleanliness | Implement effective sanitation procedures to prevent contamination, cross-contamination, and maintain a clean manufacturing environment. |
Raw Material Control | Maintain strict control over the sourcing, handling, storage, and processing of raw materials to ensure their safety and quality. |
Process Controls | Establish controls and procedures to monitor and manage critical points in the production process, ensuring consistent product quality. |
Allergen Control | Implement measures to prevent cross-contamination and allergen exposure, including segregation and proper labeling of allergenic ingredients. |
Conclusion
Good Manufacturing Practice (GMP) stands as a cornerstone in various industries, ensuring the consistent production, control, and distribution of safe, high-quality products. Whether in pharmaceuticals, food and beverages, medical devices, cosmetics, or other sectors, GMP serves to guarantee that products meet defined quality standards appropriate for their intended use. The principles of GMP revolve around stringent control, adherence to guidelines, and a commitment to excellence throughout the production lifecycle.
FAQs
Good Manufacturing Practice (GMP) is a set of guidelines and principles that ensure the consistent production, control, and distribution of safe, high-quality products in various industries, including pharmaceuticals, food, medical devices, cosmetics, and more.
GMP is crucial to maintain product quality, safety, and efficacy. It ensures that products meet specific quality standards, comply with regulations, and provide consumers with safe and effective products.
GMP applies to a range of industries, including pharmaceuticals, biotechnology, food and beverages, medical devices, cosmetics, and any other industry involved in the production of consumable or usable products.
The key principles of GMP include a Quality Management System (QMS), personnel training and hygiene, facility and equipment control, proper documentation, production and process controls, material control, validation and qualification, and quality control and testing.